Polyseal is a proven manufacturer of sealing elements in the aerocraft and defense industry and can provide optimal sealing for many applications. The materials and products suggested in this review can be mounted on anything from light to heavy land weapons to military aircraft.
Our sealing products are used in a wide range of systems including flight control, landing gear, brakes, engines, fuel control …
DESCRIPTION
Polyseal engineering expertise, material development, product range and service capabilities confirm its position as a well-known manufacturer of sealing products in the aircraft and defense industry market.
APPLICATIONS
Polyseal products are used in military aerospace and other defense industry projects and are reliable sealing solutions in a wide range of critical applications such as:
- Landing gear systems
- Flight control and management
- Braking systems
- Hydraulic user systems

DESCRIPTION
Our commitment to solving technically sophisticated applications is supported by our industry-leading portfolio of elastomeric, thermoplastic and thermoplastic composite materials. Extremely high and extremely low temperatures, chemical influences and fuel impermeability are just some of the characteristics of these applications.
APPLICATIONS
Polyseal products are used in transport and fueling equipment in aircraft fuel systems:
• Parts in contact with jet fuel
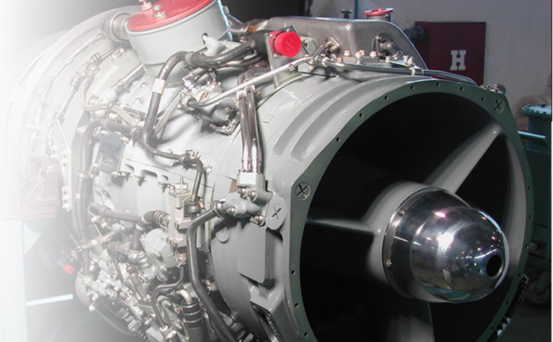
DESCRIPTION
Working with the defense sector, we have learned that precision, reliability and efficiency must be imperative in our work. Long-term cooperation and dedication to this work has produced the necessary knowledge and offered sealing solutions for the most technically sophisticated applications.
APPLICATIONS
- Hydraulic installations
- Actuators
- Shock absorbers
- Hydraulic pumps and motors
- Pneumatic installations
- Braking systems
- Driving systems
- Systems and testing equipment
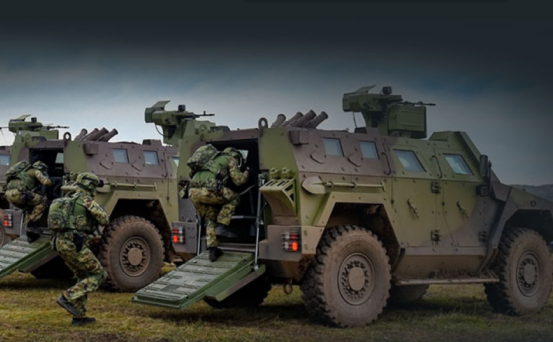
DESCRIPTION
Composite seals and bearings in the most demanding applications require different materials with specific properties, as well as their combinations. We ensure that all materials such as rubber, PTFE and other high performance materials meet the demanding specifications and are approved by users in the aerospace and defense industries.
The extremely diverse and demanding applications in aerospace and defense equipment also require an extremely wide range of speeds, operating temperatures, chemical and environmental impacts, reliability in use and long life.
Here we will describe some properties of rubber and PTFE materials that are recommended for use in these applications. Other materials are available. For more details contact us…
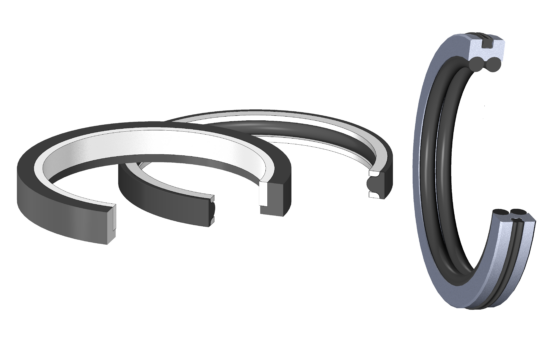
Linear speed: |
Recommended values may differ depending on seal design and operating conditions. |
Chemical compatibility |
|
Temperature range of use | Recommended elastomeric materials, rubber:
|
Low temperature |
|
High temperature |
|
Elastomeric material, Rubber
In aerospace and defense applications, many designs include rubber seals. Therefore, it is important that many parameters such as permanent deformation after compaction, media compatibility, speed, application temperature range, tolerances, etc. keep under control. Our quality assurance and 100% batch testing, ensure that the manufactured materials are in accordance with the specifications.
Here we have provided details of the rubber materials recommended for use in these applications. Other materials are available. For more details contact us…
Material Code | Suitable Rubber Base | Hardness (Shore A) | Temperature Range (oC) | Reference Specification | Media Type | Specification or Media Name | Application Information |
---|---|---|---|---|---|---|---|
N7173 | NBR | 70 | -54 to + 135 | MIL-P-25732 SNO7195 TU380051166-73 |
Petroleum | AMG –10 Hydraulic oil Low temp. (HUNT-S) |
Landing gear shock strut, Hydraulic oil Installations |
N7093 | NBR | 75 | -54 to + 135 | MIL-P-25732 SNO7195 TU380051166-73 |
Petroleum | MIL-PRF-5606 (NATO H-515) Aero Shall Fluid 4 |
Landing gear shock strut, Hydraulic oil Installations |
N7188 | NBR | 80 | -54 to + 135 | MIL-P-25732 SNO7195 TU380051166-73 |
Petroleum | MIL-PRF-5606 (NATO H-515) Aero Shall Fluid 4 |
Landing gear shock strut, Hydraulic oil Installations |
F9727 | FPM | 80 | -20 to + 230 | SNO7196 DTD5643 TU380051166-73 |
Kerosene | Jet Fuel; JP-4, JP-5, Jet-A |
Aviation Fuel Applications |
Material Polytetrafluoroethylene, PTFE
Very common solutions in application are composite seals in which, in addition to the rubber element, we also find PTFE materials as an integral part of the solution. This applications requires the highest quality pure PTFE material and also its numerous mixtures with mineral ingredients and additives. These compounds improve the basic properties of PTFE material to meet the high demands of working conditions such as linear speeds of coupled parts, very low or extremely high working temperatures, chemical compatibility of the material and the environment, etc.
Material Code | Tensile strength (Mpa) |
Elongation (%) | Hardness (Shore D) | Specific Gravity (g/cm3) | Color | Description and Applications |
---|---|---|---|---|---|---|
T1001 | 40 | 380 | 58 | 2.16 | white | Additive:Virgin PTFE Profile: Low pressure,low friction, clean systems Surface: Steel, Chrome |
T1004 | 27 | 250 | 63 | 3.08 | Greyish to dark brovn |
Additive: Bronze (medium filled) Profile: Extrusion resistance,Hydraulic/pneumatic applications.Notsuitable for water and insulation applications. Surface: Hardened Steel, Chrome, Cast iron |
T1010 | 18 | 200 | 60 | 3.91 | Light to dark brown |
Additive: Bronze (high-filled) Profile: Very high extrusion resistance and compressive strength, for linear lubricating motions. Surface: Hardened Steel, Chrome,Cast iron |
T1014 | 15 | 150 | 63 | 2.1 | Black | Additive: Carbon/Grafite Profile: Medium and high loads, V-rings Packings,Compressor ring. Ideal for water applications Surfaces: Steel, Chrome |
T1015 | 20 | 200 | 61 | 2.4 | Black | Additive: Grafite Profile: Very low wear on hard metals.Gude ring for chock absorbers Surface: Hardened steel, Chrome |
1016 | 23 | 300 | 62 | 2.2 | Black | Additive: Glass fiber (15%) Profile: Piston Rings, Buchings, Excellent abrasion and high pressure resistance Surface: Hardened steel, Chrome |
T1021 | 20 | 260 | 62 | 2.24 | Black | Additive: Glass fibers/MoS2 Profile: Rotary applications, Lip Seals, Dynamic Seals Surface: Hardened steel, Chrome |
T1030 | 22 | 250 | 62 | 2.09 | Grey | Additive: Carbon fiber Profile: Long wear life, High pressure Surface: Steel, Chrome plating |
T1035 | 15 | 200 | 60 | 1.94 | Grey | Additive: Polyimid Profile: Piston rings and Sealing elements, Self-lubricating bearing Surface: Steel, Chrome plating |